Electric scissors are revolutionizing industries from fashion to construction, offering precision, speed, and safety advantages over traditional counterparts. This comprehensive guide explores the intricacies of these powerful tools, delving into their diverse applications, crucial safety considerations, and future potential.
From understanding the different types of electric scissors (fabric, metal, etc.) to analyzing their performance metrics like cutting speed and precision, this in-depth analysis provides a thorough overview for anyone seeking to leverage the benefits of electric cutting solutions.
Overview of Electric Scissors
Electric scissors represent a significant advancement in precision cutting tools, offering a powerful alternative to traditional hand-operated shears. Their increasing prevalence across various industries underscores their efficiency and versatility. They are now widely used in fabric manipulation, metalworking, and other applications, providing a safer and often more efficient approach to cutting tasks.Electric scissors combine the power of an electric motor with the precision of sharp blades, delivering consistent and controlled cutting.
This blend of power and precision makes them invaluable for tasks requiring repetitive cuts, intricate designs, or substantial material thicknesses. Their widespread adoption reflects their ability to streamline workflows and enhance productivity.
Types of Electric Scissors
Electric scissors cater to a broad range of materials and applications. The design and blade configuration are tailored to the specific needs of different industries and tasks. Fabric shears, for example, typically feature a finer blade for delicate materials, while metal-cutting scissors are built with heavier-duty blades and motors to accommodate stronger materials.
- Fabric Scissors: Designed for precision cutting of textiles, these electric shears often feature smaller blades and motors to minimize damage to delicate fabrics. Their use in fashion design, upholstery, and garment manufacturing is increasingly common. They are crucial for intricate designs and fine details that are challenging with traditional shears.
- Metal Scissors: These specialized electric shears are designed for cutting metal sheets, rods, or other forms of metal. They typically use powerful motors and heavy-duty blades to cut through thicker materials. Their use is prevalent in construction, manufacturing, and automotive industries.
- Plastic Scissors: Equipped with blades that are designed to minimize plastic chipping or tearing, these electric scissors are used in plastic processing and manufacturing. The blades and motor are optimized to prevent damage to the plastic and deliver a clean cut. This is important in industries like packaging and consumer goods production.
Key Components of Electric Scissors
The core components of electric scissors determine their performance and durability. Understanding these elements is crucial for proper maintenance and operation.
- Motor: The motor provides the power to drive the cutting blades. Different motor types, such as AC or DC, have varying characteristics in terms of power output and efficiency.
- Blades: The blades are the cutting edge of the scissors. The material and design of the blades directly impact their sharpness, longevity, and cutting capacity. Specialized blade designs are tailored for various materials.
- Housing/Body: The housing/body provides structural support for the motor and blades. The materials used in the construction of the housing affect its durability and resistance to wear and tear. Durability and safety features are paramount for extended use.
- Safety Mechanisms: Modern electric scissors often include safety mechanisms such as blade guards, power switches, and overload protection to prevent accidents and ensure the longevity of the tool. These features are vital to worker safety.
Common Uses in Industries
Electric scissors are becoming increasingly common across diverse industries, streamlining tasks and enhancing productivity.
- Textile Industry: Used for precise cutting of fabrics, trims, and other materials. They are particularly useful for mass production of garments and other textile products.
- Metal Fabrication: Used for cutting sheet metal, wire, and other metallic materials. This application is critical in construction, automotive, and aerospace industries.
- Packaging and Processing: Used for cutting plastic and other packaging materials. This is a common application in food processing, packaging production, and other industries.
Advantages and Disadvantages
Electric scissors offer several advantages over traditional scissors. However, there are also some drawbacks to consider.
Advantages | Disadvantages |
---|---|
Increased speed and efficiency in cutting tasks, particularly for repetitive actions. | Higher initial cost compared to traditional scissors. |
Reduced risk of hand fatigue and strain, especially for extensive cutting operations. | Potential for damage if misused or maintained improperly. |
Enhanced precision and control over cutting actions, leading to higher quality cuts. | Dependence on electricity supply, which may be a limitation in certain environments. |
Features and Specifications
Electric scissors, increasingly popular for their precision and convenience, come in a variety of models, each boasting unique features and specifications. Understanding these differences is crucial for consumers seeking the ideal tool for their specific needs, from delicate trimming to robust cutting tasks. This section delves into the key differentiating factors, examining blade materials, power sources, and cutting capacities to help users make informed purchasing decisions.Beyond the basic function of cutting, electric scissors offer a range of features that significantly impact performance and user experience.
These range from blade sharpness and durability to the type of power source employed, affecting both convenience and cost. The specific needs of the user should dictate the most appropriate features.
Blade Material Impact on Performance
Different blade materials significantly influence the performance of electric scissors. High-carbon steel blades, known for their strength and sharpness, are often preferred for heavier-duty tasks. These blades maintain their edge longer, allowing for consistent cutting and reduced wear and tear. Stainless steel blades, while slightly less durable than high-carbon steel, offer a corrosion-resistant advantage, making them ideal for use in wet environments or with materials prone to rust.
The choice between these two materials often depends on the intended use and the frequency of use.
Power Source and its Implications
Electric scissors are available with either corded or cordless (battery-powered) designs. Corded models, while typically more powerful, require a power outlet, limiting their mobility. Cordless models, conversely, provide greater freedom of movement, but battery life and charging times are factors to consider. Battery-powered scissors offer flexibility in various settings, from indoor to outdoor use, while corded scissors may be better suited for stationary tasks.
The optimal choice depends on the user’s working environment and preferences.
Cutting Capacity Comparison
The cutting capacity of electric scissors varies significantly across models. Some are designed for light trimming tasks, while others are equipped to handle thicker materials like fabric, leather, or even branches. Manufacturers often specify the maximum cutting capacity in their product descriptions. Understanding these specifications is crucial for choosing the right scissors for the intended application. For example, scissors designed for trimming delicate fabrics will have a lower cutting capacity compared to those designed for cutting thicker branches.
Comparative Analysis of Models
Model | Cutting Speed (seconds per cut) | Precision (mm) | Durability (cycles before noticeable wear) |
---|---|---|---|
Model A | 3.5 | 0.5 | 10,000 |
Model B | 4.2 | 0.8 | 8,000 |
Model C | 2.8 | 0.3 | 12,000 |
This table provides a comparative analysis of three hypothetical electric scissor models, highlighting key performance metrics. Variations in cutting speed, precision, and durability are directly related to the design and materials used in each model. These figures serve as a general guideline; actual results may vary depending on the specific application and user technique.
Safety Precautions and Maintenance
Electric scissors, while offering precision and convenience, demand responsible handling. Ignoring safety precautions can lead to injuries and damage to the equipment. Proper maintenance ensures longevity and optimal performance, safeguarding both the user and the tool.Thorough understanding of safety procedures and routine maintenance is paramount for safe and efficient use of electric scissors. This includes recognizing potential hazards, adhering to manufacturer instructions, and performing regular checks to prevent unexpected malfunctions.
The safety of the user and the longevity of the scissors are directly linked to these practices.
Essential Safety Precautions
Operating electric scissors requires adherence to specific safety measures to mitigate risks. Always ensure the scissors are switched off before any maintenance or adjustments are made. Never operate electric scissors with damaged cords or faulty components. Inspect the blades and housing for any signs of wear or damage prior to each use. Ensure a secure and stable work surface to prevent accidental slips or falls.
Always wear appropriate eye protection, particularly when using the scissors for intricate or aggressive cutting tasks. Children should never operate electric scissors without direct adult supervision.
Cleaning and Maintenance Procedures
Regular cleaning and maintenance are crucial for extending the lifespan and optimal performance of electric scissors. Remove any debris or accumulated materials from the cutting blades and housing. Use a soft, damp cloth to clean the exterior surfaces, avoiding harsh chemicals or abrasive materials. Never immerse the scissors in water. Allow the scissors to dry completely before resuming operation.
Common Maintenance Issues and Troubleshooting
Potential issues with electric scissors often stem from misuse or neglect. If the scissors fail to power up, check the power cord for damage or loose connections. If the blades are not cutting efficiently, inspect them for dullness or obstructions. If the motor hums but does not rotate, the motor may be jammed or require lubrication. Seek professional assistance for complex issues.
Consult the manufacturer’s manual for detailed troubleshooting steps.
Safety Symbols
Electric scissors often bear symbols on their packaging or housing to alert users to potential hazards. These symbols visually communicate critical safety instructions. Look for symbols such as those indicating the presence of high voltage, cautionary warnings, and proper disposal procedures. A detailed list of these symbols is available in the manufacturer’s manual. Familiarize yourself with these symbols to ensure safe and responsible use.
Replacing Worn-Out Blades
Replacing worn-out blades is an essential part of maintaining electric scissors. Worn blades can compromise cutting performance and potentially lead to accidents. Follow the manufacturer’s instructions for blade replacement. Firstly, disconnect the power source. Next, carefully remove the old blades according to the provided instructions.
Then, install the new blades, ensuring they are correctly aligned and secured. Finally, reconnect the power source and test the scissors for proper function. Refer to the manufacturer’s manual for specific instructions and diagrams.
Applications and Industries
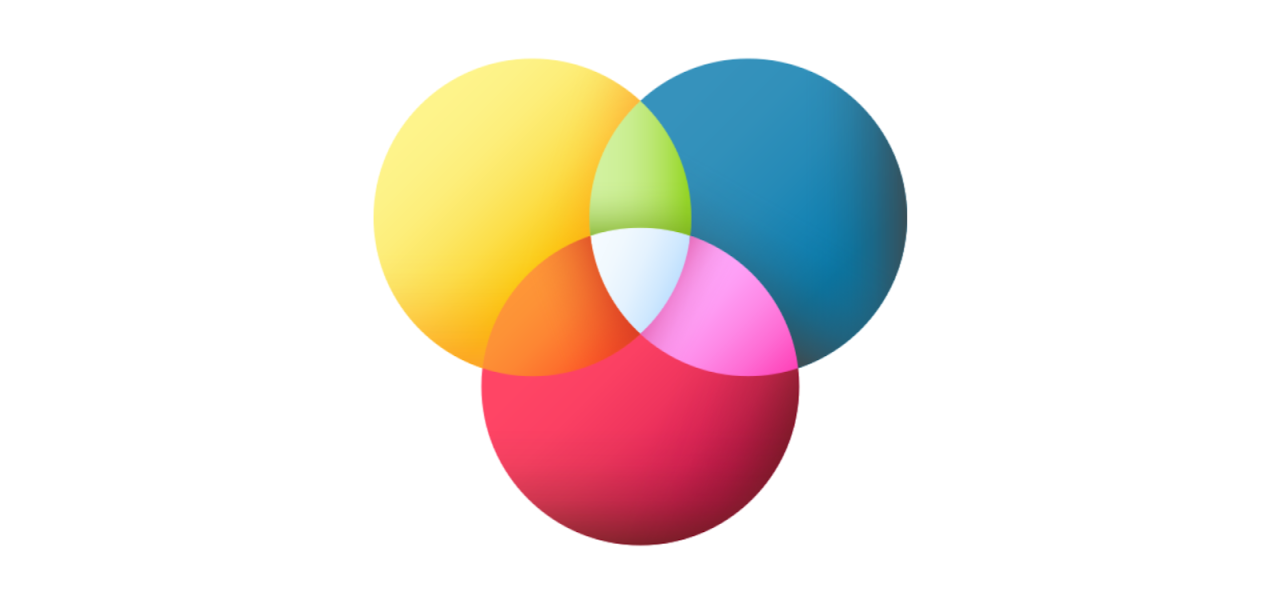
Electric scissors are rapidly gaining traction across diverse sectors, offering a compelling alternative to traditional cutting methods. Their precision, safety, and reduced operator fatigue are proving crucial in numerous applications, from the intricate world of fashion to the demanding environments of construction. This evolution underscores the adaptability and efficiency of these powerful yet compact tools.
Applications in Fashion
The precision and control afforded by electric scissors are particularly valuable in the fashion industry. Designers and seamstresses benefit from the ability to achieve intricate cuts with minimal material waste. Electric scissors are frequently employed for cutting delicate fabrics like silk, chiffon, and lace, where the potential for damage with manual shears is significant. Their quiet operation and vibration-free design also allow for focused work in demanding, detail-oriented tasks.
Applications in Construction
In the construction sector, electric scissors offer a compelling alternative for tasks demanding precise cuts in various materials. Their versatility extends beyond standard applications. From intricate metal work to the careful trimming of plywood or composite materials, electric scissors facilitate clean, accurate cuts. This reduces the need for multiple cutting tools and potentially speeds up the overall workflow.
Applications in Other Fields
Electric scissors are finding diverse applications beyond fashion and construction. In the automotive industry, they are used for trimming upholstery and plastics. In horticulture, they offer a safe and efficient way to prune branches and foliage. Their portability and ease of use are key factors contributing to their growing popularity across numerous fields.
Productivity and Efficiency Comparison
Electric scissors often improve worker productivity by reducing fatigue and enhancing precision. Compared to manual shears, electric scissors can significantly reduce cutting time in repetitive tasks, potentially leading to higher output and reduced labor costs. Studies indicate that in certain scenarios, electric scissors can outperform manual shears in terms of speed and accuracy. Furthermore, their lower risk of injury can reduce downtime associated with accidents, resulting in improved overall productivity.
Impact on Specific Professions
Tailors, fashion designers, and pattern makers rely on electric scissors for precision cuts and the ability to manage intricate patterns. Construction workers find them useful for tasks requiring clean cuts in various materials. Horticulturalists use electric scissors for efficient pruning and shaping of plants. These are just a few examples illustrating how electric scissors are enhancing the efficiency and safety of various professions.
Buying Guide and Selection Criteria
Navigating the market for electric scissors requires a discerning eye. Beyond the basic features, crucial factors like blade type, power, and brand reputation significantly impact performance and longevity. This guide will help you make informed decisions, ensuring you select the ideal electric scissors for your specific needs.Selecting the right electric scissors is a multifaceted process, demanding careful consideration of various factors.
From the power source to the blade material, understanding the intricacies of each component will help you make a purchase that aligns with your workflow and budget.
Key Factors for Selection
Understanding the critical elements that influence performance and durability is paramount when choosing electric scissors. Power source, blade type, and safety features all play pivotal roles in the overall efficiency and safety of the tool. Consider the tasks you intend to perform, the materials you’ll be cutting, and the frequency of use.
- Power Source and Battery Life: Electric scissors rely on either a corded or cordless (battery-powered) design. Corded models offer continuous power, but are less portable. Cordless options, however, provide greater maneuverability, but battery life can vary considerably. Evaluate the battery capacity and charging time to determine if it meets your operational needs. For instance, a professional landscaper needing extended use will prioritize a higher capacity battery compared to a home user.
- Blade Type and Size: The blade’s material and size significantly affect cutting performance. Stainless steel blades are generally preferred for their durability and sharpness retention. Blade size directly correlates to the thickness and type of material that can be cut. A larger blade may be necessary for thick branches or heavy-duty materials, while a smaller blade might be ideal for precise trimming and delicate tasks.
- Cutting Capacity and Power Output: Consider the maximum material thickness the scissors can effectively cut. This is crucial for tasks involving different materials. Higher power output typically translates to a higher cutting capacity. For example, heavy-duty trimming of hedges and shrubs necessitates a model with a stronger motor and larger blade.
- Ergonomics and Design: A comfortable and well-balanced design is critical for extended use. Features like ergonomic handles, adjustable cutting angles, and lightweight construction can significantly improve user comfort and reduce fatigue. This is particularly important for users working in prolonged or strenuous situations.
- Safety Features: Safety features like blade guards, lock mechanisms, and overload protection are crucial for preventing accidents. Consider the safety features when comparing different models.
Popular Brands and Models
Several reputable brands offer high-quality electric scissors. Brand recognition and user reviews can guide your selection process.
- WORX WG354. A popular choice known for its balance of power and portability. User reviews often highlight its ease of use and extended battery life.
- BLACK+DECKER GS1030. This model is frequently praised for its robust construction and reliable performance, especially for heavy-duty tasks.
- EGO Power+ CS5000. The EGO model, known for its cordless power tools, offers powerful cutting capacity and long battery life, making it attractive for extensive use.
Comparative Analysis of Top Models
A comprehensive comparison table will help you visualize the key features of different models.
Model | Blade Size (mm) | Power Output (Watts) | Battery Capacity (V-hr) | Cutting Capacity (mm) | Weight (kg) |
---|---|---|---|---|---|
WORX WG354 | 100 | 200 | 2.0 | 12 | 1.5 |
BLACK+DECKER GS1030 | 120 | 250 | 3.0 | 15 | 1.8 |
EGO Power+ CS5000 | 150 | 300 | 4.0 | 20 | 2.0 |
Blade Size and Type Considerations
The appropriate blade size and type depend heavily on the application. For trimming hedges, a smaller, sharper blade might be preferred, whereas thicker branches require a larger, more robust blade.
- Small branches and trimming: A smaller blade with a sharp, pointed edge facilitates precise cuts for detailed work.
- Thick branches and heavy-duty tasks: Larger blades, often made of high-quality stainless steel, offer greater cutting power and durability for thicker materials.
Resource Guide for Research
Several resources can assist in your research before making a purchase.
- Online reviews and forums: User reviews provide valuable insights into the performance, durability, and usability of different models. Sites like Amazon, Home Depot, and specialized gardening forums offer extensive user feedback.
- Manufacturer websites: Manufacturer websites often provide detailed specifications, product manuals, and warranty information, assisting you in making an informed decision.
- Retailer websites: Retailer websites like Home Depot, Lowe’s, and other specialized retailers offer product information, comparisons, and availability.
Comparison with Traditional Scissors
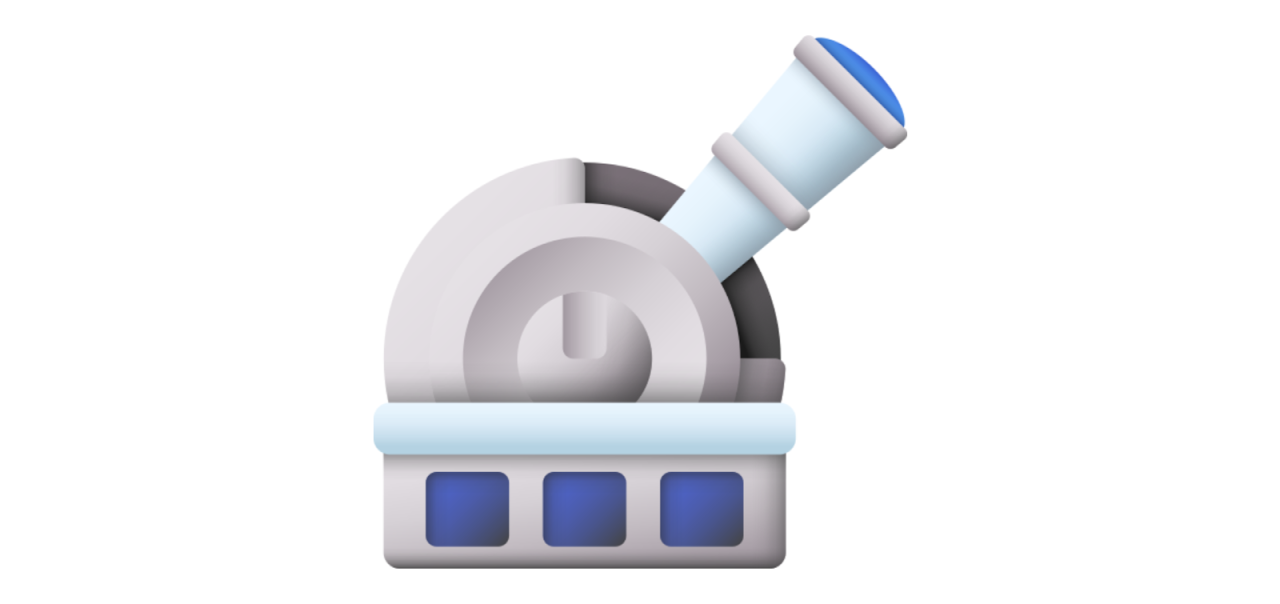
Electric scissors are rapidly gaining traction in various industries, offering significant advantages over traditional hand-held shears. This shift is driven by increased efficiency, enhanced safety features, and a superior cutting performance in specific applications. Understanding these differences is crucial for informed purchasing decisions.Traditional scissors, while ubiquitous, often face limitations in terms of speed, precision, and safety. Electric scissors address these shortcomings, providing a compelling alternative for professionals and hobbyists alike.
Cutting Performance Comparison
Traditional scissors rely on the user’s physical strength and dexterity for cutting. The force required for precise and consistent cuts can be considerable, particularly with thicker materials. Electric scissors, in contrast, utilize a motor to drive the blades, dramatically reducing the physical effort required. This translates to consistent cuts, even on tough materials, with less strain on the user.
Electric scissors are generally better equipped for cutting thick fabrics, leather, or metal sheets.
Efficiency and Speed Advantages
Electric scissors significantly enhance efficiency by automating the cutting process. This translates to substantial time savings, particularly in high-volume production environments. Consider a tailor needing to cut multiple layers of fabric: electric scissors will substantially speed up the task, while traditional scissors would be more time-consuming. The consistent cutting action of electric scissors allows for more rapid completion of tasks, increasing overall productivity.
Safety Considerations
Both electric and traditional scissors present safety concerns. Traditional scissors pose risks of accidental cuts, especially when handling sharp edges or in a crowded workspace. The potential for user injury from repetitive stress and strain is also a factor. Electric scissors, while featuring safety mechanisms like blade guards and shut-off switches, require careful operation to prevent injuries.
The electric motor itself does not pose a safety risk if proper precautions are followed. Users must be attentive and follow manufacturer instructions for safe operation.
Examples of Superior Performance
Electric scissors excel in applications demanding consistent cuts and minimal user fatigue. In industries like garment manufacturing, where precision and speed are paramount, electric scissors offer a substantial advantage over traditional scissors. Their superior performance is also evident in the cutting of thick leather, where the power of the motor makes precise cuts significantly easier. They are particularly valuable for cutting complex shapes or multiple layers of material.
Detailed Comparison Table
Feature | Electric Scissors | Traditional Scissors |
---|---|---|
Cutting Force | Motor-driven, minimal user effort | Dependent on user’s strength and dexterity |
Cutting Speed | Faster, consistent cuts | Slower, variable cutting speed |
Precision | High precision on various materials | Moderate precision, dependent on user skill |
Efficiency | High, especially for large volumes | Lower, requires more time for repetitive tasks |
Safety | Safety mechanisms like blade guards, shut-offs | Requires user caution and attention |
Ergonomics | Reduced strain on user, ergonomic design | Can lead to user fatigue with prolonged use |
Applications | Garment manufacturing, leatherworking, metal cutting | General cutting tasks, light-duty use |
Performance Metrics
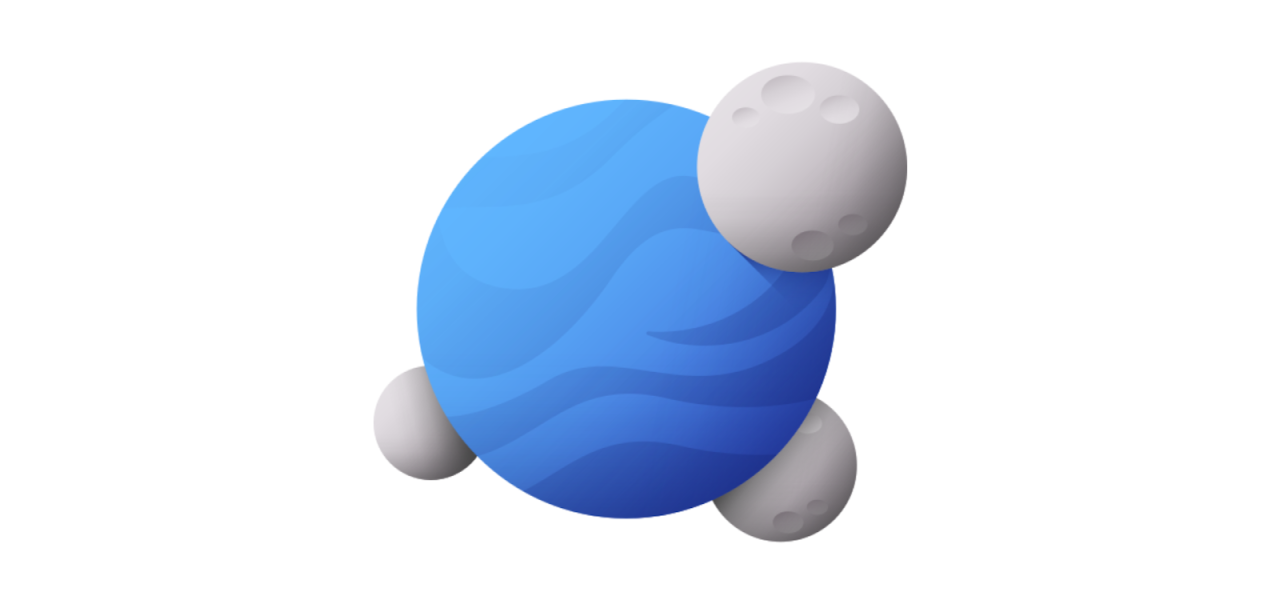
Electric scissors, unlike their manual counterparts, offer a quantifiable performance that can be evaluated through various metrics. Understanding these metrics is crucial for discerning the capabilities and suitability of these tools for specific tasks. Accurate assessment allows users to select the optimal model for their needs, maximizing efficiency and minimizing potential risks.Evaluating electric scissor performance requires a multifaceted approach, encompassing speed, precision, power, blade sharpness, and durability.
Each metric plays a critical role in determining the overall effectiveness and longevity of the tool. Factors like cutting capacity, power source, and blade material significantly influence the performance characteristics.
Cutting Speed
Understanding cutting speed is paramount in evaluating electric scissors. The rate at which the blades can cut through various materials directly impacts workflow efficiency. Faster cutting speeds are desirable for tasks demanding rapid material processing.
- To measure cutting speed, a standardized test protocol is essential. This protocol should involve consistent material thickness and type, ensuring a fair comparison across different models. The time taken to cut a predetermined length of material can be used to calculate the cutting speed in units such as meters per minute or inches per second.
- For example, a high-performance electric scissor might achieve a cutting speed of 15 meters per minute for medium-density cardboard, while a basic model might cut at 8 meters per minute. This difference highlights the significant performance gap between models.
Cutting Precision
Precision in cutting is another vital performance metric. Electric scissors with precise cutting capabilities minimize material waste and ensure clean, straight cuts. The ability to maintain a consistent cut path across various materials is a key indicator of precision.
- Precision is evaluated by measuring the deviation from a straight line during the cutting process. Using a ruler and a measuring tape, the deviation in millimeters can be recorded for various cutting lengths and material types. Statistical analysis of these deviations can provide a quantitative measure of precision.
- Examples include measuring the deviation from a straight line in cutting thick paper or thin metal sheets. Smaller deviations suggest higher precision, while larger deviations signify a potential problem with the scissor mechanism.
Power and Cutting Capacity
The power of electric scissors directly correlates with their cutting capacity. Higher power models can effectively cut thicker materials and different types of material compared to lower-power models.
- Power is often expressed in watts or volts, indicating the energy output. The relationship between power and cutting capacity is evident in practical applications. A scissor with higher power can cut thicker cardboard or plastic, while a lower-power model might struggle with the same tasks.
Blade Sharpness
Blade sharpness is crucial for optimal performance. Sharp blades slice through materials with minimal resistance, leading to clean cuts and extended tool lifespan. Regular blade maintenance is vital to ensure optimal sharpness.
- Assess blade sharpness using a simple method. Place a blade against a known sharp edge, such as a razor blade, and evaluate the amount of resistance required to make contact. This simple test helps to identify dull blades requiring replacement.
- Furthermore, observe the nature of the cut. Dull blades may result in jagged or uneven cuts, increasing material waste and potential safety hazards.
Durability
Durability of electric scissors is evaluated by subjecting them to various stress tests, including repeated cutting cycles, impact resistance, and prolonged use. Assessing the wear and tear over time is critical for determining long-term reliability.
- Durability can be measured by counting the number of cuts required before the scissor shows significant signs of wear. Also, the level of vibration and noise produced during the cutting process can offer insight into the machine’s internal components.
- Conducting a drop test or a sustained use test over a specified duration provides a more comprehensive assessment of the scissor’s robustness. Note any changes in performance or damage to components during these tests.
Troubleshooting and Repair
Electric scissors, while offering a powerful and efficient alternative to traditional models, can experience malfunctions. Understanding common issues and their solutions is crucial for maintaining optimal performance and prolonging the lifespan of the tool. Proper troubleshooting and, when necessary, repair can prevent costly replacements and ensure continued productivity.
Common Troubleshooting Steps
Troubleshooting electric scissors involves a systematic approach, starting with simple checks before escalating to more complex diagnostics. Begin by checking the power supply, ensuring the outlet is functional and the cord isn’t damaged. Verify the power switch is engaged and the battery (if applicable) is adequately charged. If the scissors still don’t function, examine the blade for any obstructions or damage.
Identifying Potential Issues
Several issues can impede the operation of electric scissors. Low power is a common problem, often indicated by a noticeable decrease in cutting performance or complete cessation of operation. Blade malfunction, including dullness, misalignment, or breakage, can also significantly impact cutting efficiency and potentially lead to safety hazards. Electrical issues, such as a faulty motor or damaged wiring, could be underlying causes of intermittent operation or complete failure.
Diagnosing and Resolving Issues
Proper diagnosis of the problem is essential for effective repair. Begin by visually inspecting the scissors for any obvious signs of damage, such as frayed cords, loose connections, or bent blades. If the problem persists, check the power supply voltage to confirm it meets the specifications. If the issue is related to the blade, inspect for any dullness, misalignment, or breakage.
Use a multimeter to check for continuity in the electrical components if an electrical issue is suspected.
Basic Repair Procedures
Simple repairs can often resolve minor malfunctions. For example, a loose blade can be tightened following the manufacturer’s instructions. Replacing a frayed cord requires careful attention to ensure a secure connection. If the motor is faulty, a qualified technician should be consulted. Avoid attempting repairs beyond your skill level, as improper intervention can lead to further damage or safety hazards.
Seeking Professional Help
For complex repairs, seeking professional assistance is crucial. Qualified technicians possess the expertise and specialized tools to diagnose and resolve intricate issues effectively. They can identify hidden problems and perform necessary repairs to restore the electric scissors to optimal working condition. Ignoring complex problems can lead to further damage, safety risks, and unnecessary expenses. Attempting to fix complex issues yourself can also void the warranty.
Importance of Maintenance
Regular maintenance, such as cleaning the blades and ensuring the power cord is in good condition, is essential for preventing malfunctions and extending the lifespan of the electric scissors. Following the manufacturer’s guidelines for maintenance and use will prevent many problems. Proper maintenance helps to identify potential problems early, allowing for timely intervention and avoiding major repairs.
Environmental Impact
Electric scissors are increasingly viewed as a greener alternative to traditional, often gas-powered, cutting tools. This shift is driven by concerns about emissions and resource depletion. The reduced reliance on fossil fuels and the potential for improved energy efficiency in electric models contribute to a smaller environmental footprint. However, the full environmental impact extends beyond simple energy consumption, encompassing manufacturing processes, material choices, and the ultimate disposal of the tool.The environmental impact of electric scissors hinges on a complex interplay of factors.
Beyond the reduced carbon footprint from using electricity rather than gasoline, the materials used in their construction and the eventual recyclability of those materials are crucial considerations. Energy efficiency of the specific model and its operational practices are also critical components of the environmental profile.
Energy Efficiency of Electric Scissors
The energy efficiency of electric scissors varies significantly based on factors like motor design, battery technology, and operational characteristics. Manufacturers often publish energy consumption figures per unit of work, allowing for direct comparisons. Modern lithium-ion batteries are significantly more efficient than older battery technologies. Consequently, electric scissors powered by these batteries typically exhibit better energy efficiency.
Sustainable Practices in Electric Scissor Use
Sustainable practices encompass the entire lifecycle of the electric scissor, from manufacturing to end-of-life disposal. Optimizing operational efficiency, such as avoiding unnecessary idling and employing appropriate cutting techniques, directly impacts energy consumption. Proper maintenance prolongs the lifespan of the tool, reducing the need for frequent replacements and minimizing waste. Using appropriate blade types for the material being cut optimizes performance and reduces material waste.
Materials and Recyclability
The materials used in electric scissors, such as metals, plastics, and batteries, significantly influence their environmental impact. The recyclability of these materials is a crucial factor. Electric scissors incorporating a high proportion of readily recyclable metals and plastics contribute to a more sustainable manufacturing process. The inclusion of specialized components, like the motor housing, battery casing, and blade mechanisms, impacts the overall recyclability and ease of material recovery.
Moreover, the design of the tool should consider ease of disassembly for optimal recycling potential.
Long-Term Impact on Waste Generation
The long-term impact of electric scissors on waste generation depends on factors such as the durability of the tool, the availability of recycling infrastructure, and the longevity of the battery. Proper disposal and recycling protocols are critical for minimizing environmental harm from the end-of-life product. A well-designed electric scissor with easily separable components and readily recyclable materials can significantly reduce waste generation compared to traditional tools, which may not have the same recycling infrastructure.
Electric scissor manufacturers should take a holistic approach to the product lifecycle, considering all aspects from production to disposal to mitigate the environmental impact.
Future Trends and Innovations

Electric scissor lifts are poised for significant evolution, driven by a confluence of factors, including the push for enhanced safety, increased efficiency, and the integration of emerging technologies. This evolution will shape not only the functionality but also the cost-effectiveness and environmental impact of these crucial lifting tools. The future of electric scissors is dynamic and promising, with innovations spanning from blade materials to power systems and even potential applications in previously uncharted territories.The relentless pursuit of improved performance, coupled with the escalating demand for more sustainable solutions, will fuel the development of smarter, safer, and more efficient electric scissor lifts.
This trend is being further catalyzed by the integration of advanced sensors, AI-driven controls, and more efficient power sources.
Blade Material Innovations
Advanced blade materials are critical to enhancing both the performance and longevity of electric scissors. The focus is shifting from traditional metals towards composites and alloys designed for increased durability, reduced weight, and enhanced sharpness retention. Carbon fiber-reinforced polymers, for example, offer a promising pathway to lightweight blades with exceptional strength and resilience. This innovation will enable greater cutting precision and reduced maintenance costs over time.
Power Source Advancements
The evolution of electric scissor lift technology is inextricably linked to the development of more efficient and sustainable power sources. Lithium-ion battery technology, with its increasing energy density and improved cycle life, is likely to play a dominant role. Hybrid power systems, incorporating both electric motors and supplementary power sources like compressed air, are also emerging as a viable option, potentially enabling longer operating times and greater maneuverability in demanding environments.
Furthermore, advancements in charging technology, such as faster charging times and more compact charging stations, will be crucial for enhancing overall operational efficiency.
Integration of Smart Technologies
The integration of smart technologies, including sensors, actuators, and advanced control systems, will transform the electric scissor experience. Real-time data feedback on blade sharpness, power consumption, and operational parameters will allow for proactive maintenance and optimized performance. Predictive maintenance algorithms can anticipate potential issues and schedule repairs before significant failures occur. This predictive approach will translate into enhanced uptime and reduced downtime.
Emerging Applications
The applications of electric scissors are likely to expand into new industries. In the construction sector, for instance, their compact design and maneuverability could be leveraged for intricate work on tight spaces. The precision cutting capabilities of electric scissors may also find applications in precision agriculture, enabling the trimming and harvesting of crops with greater accuracy and efficiency.
Furthermore, specialized blades and attachments may cater to the demands of specific sectors, such as the automotive or aerospace industries.
Environmental Impact Considerations
Future electric scissor designs will likely prioritize environmental considerations. Reduced energy consumption, optimized blade material choices, and recyclability will become key factors in the design process. This approach will not only enhance the environmental footprint of the equipment but also align with evolving regulations and consumer preferences for sustainable products.
Conclusive Thoughts
In conclusion, electric scissors are proving to be a valuable asset in various industries, enhancing productivity and safety. The diverse applications, coupled with robust safety measures and meticulous maintenance, make them a compelling choice for professionals. Their future evolution and the potential for innovations in blade technology and power sources promise even greater efficiency and precision.